デルタ社が完成した5Gスマート工場を一般公開し、5Gの高速通信と低遅延を活用して、AMR、自動プラグインマシン、AR・VRと組み合わせて、スマートな生産環境を実証したことが話題になっており、広く注目されています。
2021年3月30日、台湾の桃園市亀山工業区に、デルタ社(https://www.deltaww.com/)市内初の5Gスマート工場が公開されました。
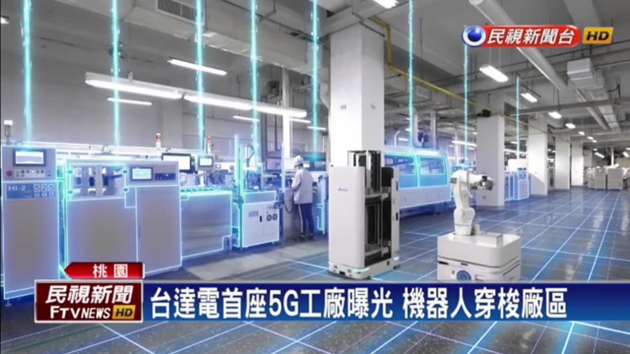
Standard Robotsは、柔軟な物流ソリューションを提供する企業の一つとして、デルタ社のコスト削減、効率化、スマート製造を実現するためのスマート工場の構築を支援してきました。
デルタ社の台湾工場の自動化は以前から実施されていましたが、このままでは現在のように少量多品目のフレキシブルな生産を対応するには不十分と考えているそうです。 少量多品目の自動化は製造業界としては理想ですが、その実現はかなり困難である、一方で、現場での頻繁なライン変更は時間の無駄であり、非常に不経済です。また、世界の製造業はかつては中央集権的でしたが、今後は市場に移動して生産を行うため、インテリジェントで柔軟な生産ラインが必要となります。
5Gの発展は、スマート工場の構築に可能性をもたらしました、モバイル機器とAMRを連携させて精密な制御を行い、ロボットアームを搭載して生産ラインとの動きを調整したり、VRやARによる人と機械の連携で遠距離指令や機械のメンテナンス、資材の配送などを行うことで、スマート工場の構築に十分な技術的サポートを提供します。
スマート工場の物流に求められるのは、柔軟性とインテリジェント性です。 デルタ社がFar EasTone社、マイクロソフト社、PTC社と共同製作した5Gスマート工場のデモラインには、Standard Robotsが開発・製造したAMRが採用され、5Gの高速通信に対応し、柔軟性・効率性・安定性を提供、スマート工場の物流ニーズに応えています。
01.プロジェクト背景
1971年に中国・台湾で設立されたデルタ電子は、売上高が10年連続で1位となっている世界No.1のコンピューター用電源メーカーであり、デルタ社の電源は世界で使用されているサーバーの2台に1台、PCは3台に1台が採用されています。デルタ社は2017年から工場はシンプル化(SIMPLIFY)、標準化(STANDARDIZE)、モジュール化(MODULARIZE)、デジタル化(DIGITALIZE)、バーチャル化(VIRTUALIZE)、自動化(ROBOTICISE),を目指してきました。
デルタ社は、頻繁な物流輸送と高い人件費、手作業によるエラーの発生、ライン末端の資材在庫過多といった課題があり、スマート工場構築のためにインテリジェントで柔軟な物流ソリューションを求めていました。
今回のスマート工場では、自動搬送装置(Rapid Transformable Machine、RTM)、自動搬送ロボット(AMR)、自律移動装置の協働ロボット(AMR+COBOT)、および仮想現実と混合現実(混合現実、MR)/拡張現実(拡張現実、AR)を使用して、組み立てトレーニング、操作支援、視覚機器の制御と管理、およびその他のインテリジェント機能を構築しました。
新設されたデルタ社の工場では、16の自動搬送装置SMTラインがあり、倉庫と工場の生産ラインの間でマガジンの完成品を移動させるために、スタンダードロボット社の自動搬送ロボットが導入されました、工程間の搬送を担うロボットはすべてStandardRobots社のものを採用されました。
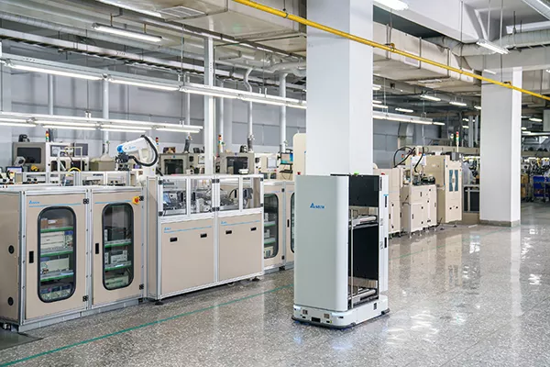
02.プロジェクトの課題
フィーダーの高さが安定しない
SMTラインでのSMTフィーダーの高さが一定でないため、標準化された製品では個々のニーズに合わせることが難しい。
高いドッキング精度が必要
AMRから生産ラインへのドッキングの精度が非常に高く、±5mm以内に収める必要あり。
機器の高い安定性
システムや機器の信頼性や安定性を大幅に調整した上で、99.5%以上の成功率達成が必須。
システムの高い適応性の要求
生産作業量に応じてロボットリソースを柔軟にスケジューリングする必要があり、生産ラインやプロセスが変更された場合には、新しいドッキング要件にシームレスな対応が求められる。
03.解決策
課題解決のため、以下機材を導入しました。
・Oasis-SMT-A2モデルAMR…8台
・倉庫自動ドッキングステーション…2セット
・自動充電器…3台
・サーバー…1台
・ネットワークソリューション…1セット
上記機材を使用し、MatrixデプロイメントソフトウェアとFMSマルチマシンスケジューリングシステムとを組み合わせることで、マガジンフレームをワークショップ内の16のSMT生産ラインに自動的に配送し、倉庫とSMT生産ライン間の完全自動ドッキングを実現しました。
04.ワークフロー
1、SMT生産ラインの資材が不足すると、MESシステムがFMSディスパッチにタスクを送信、AMRが倉庫に向かいます。自動ローディングドックからマガジン資材をピックアップし、SMT生産ラインの資材要求ポイントへ搬送します。
2、AMRと生産ラインのヘッドフィーダーを自動ドッキングし、下段はフルマガジンを機械に送り、上段は空のマガジンをカートに回収します。
3.AMRが空のマガジンを自動ピックアップカウンターに送り、ピックアップカウンターから倉庫に搬送します。
4、SMTラインの末端でフルマガジンが完成すると、MESシステムはFMSにタスクを送信し、AMRを倉庫に派遣して自動ローディングドックから空のマガジンを受け取り、生産ラインの末端まで走ってフルマガジンを取り出し、上段では空のマガジンをラインの末端のフィーダーに送ります。
5、AMRは完成品を倉庫の自動ピックアップテーブルに搬送後、タスクを終了します。
05.メリット
迅速な導入プロセス
MESシステムとシームレスにドッキングすることで、デジタルでインテリジェントな生産管理を実現します。既存のラックを交換する必要がなく、サイトの変更も不要なため、変更にかかるコストを大幅に削減できるだけでなく、導入期間も短縮でき、通常の生産に影響を与えません。
柔軟性と信頼性
AMRはレーザーSLAM法を採用しており、地上に測位設備を敷設する必要がなく、走行経路を柔軟に変更することができ、生産ラインの変更にも迅速に対応することができます。30日間の試運転で合計12,000回のミッション処理を行い、異常が発生したのは16回のみで、成功率は99.87%となり、無事目標値を達成しました。
安全性と安定性
複雑な環境下でのAMRの測位精度はミリメートルレベルに達し、正確な測位により、より安定した信頼性の高い輸送とドッキングを実現します。マルチレベルの安全保護対策を備え、スマート工場における人と機械の安全性を確保します。また、アイドル時の自動充電により、24時間連続稼働を実現しました。
06.プロジェックの価値
・生産性効率
手作業に比べて89%生産効率が向上しました。
・人件費削減
ワークショップの資材配布スタッフを削減し、昼夜交代で合計6名のみの配置となりました。
・エラー率減少
手動作業のエラー率2.94%が0%になりました。
・情報の透明性
MESシステムに接続して、工場の資材の状態をリアルタイムで監視できます。
・スペースの節約
元々ラインの端には多くの資材が積まれていましたが、今ではそのスペースを占有する必要もなく、ワークショップの5Sが大幅に改善されました。
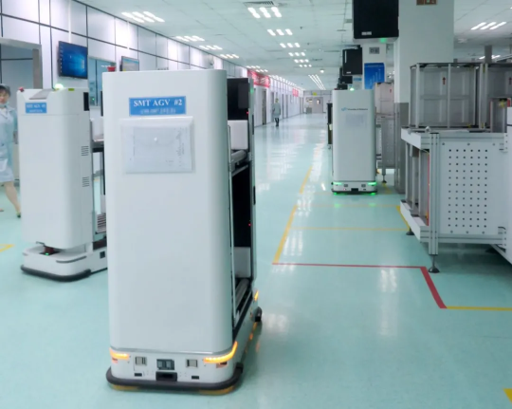
Standard Robotsが提供する柔軟な物流ソリューションにより、デルタ社の5Gスマートで実証した生産ラインは、3ヶ月間で一人当たりの生産量が70%近く増加し、単位面積当たりの生産ラインの生産量が75%増加しました。
デルタ社の社長である張迅海氏は、この投資が1年以内に回収され、無駄な作業を減らし、従業員の自己価値の向上と実現、製造業の競争力を高め、インダストリー4.0への変革のペースを加速させることができると予測しています。
5G対応AMRを受注開始
2021年7月より、
スタンダードロボットは日本マーケット向けに5Gに対応した自動搬送ロボットの受注を開始します。詳細は テクトレ株式会社 までお問い合わせくださいませ。
問い合わせフォーム:https://techtrade.jp/contact-us/
製品情報:https://standard-robots.jp/products/smt/
製品相談窓口:https://standard-robots.jp/partners/